25 November 2019 – Ecochlor is excited to announce the formalization of an agreement to represent NanoVapor in the maritime industry. The product launch will be at Marintec China with a NanoVapor unit on display at the Ecochlor Stand N3D5N.
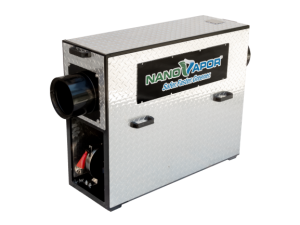
The NanoVapor technology dramatically improves crew safety while significantly reducing time and any environmental pollution related to gas-freeing VOCs from cargo or bunker tanks. A single application can continue to suppress VOCs for days. The NanoVapor degassing process is more cost effective than traditional methods of cleaning these types of tanks.
A NanoVapor unit consists of two components: a nano-suppressant liquid, TankSafe and a portable delivery unit, Model ST-1000. The delivery unit operates using a compressed air source to create a high-flow air stream to inject the suppressant molecules into the tank. The molecular suppressant works up to 90% faster than current enclosed space procedures to quickly suppress VOC evaporation.
Stuart Bayliss, service manager at Kidderminster Petroleum Services shared his experiences: “The NanoVapor solution is by far the easiest, quickest and less expensive way to make a tank completely safe to work on. By using NanoVapor, the downtime of each tank is one day. By using alternative methods, such as water filling, the downtime can be as much as three days …”
TankSafe is engineered from renewable materials, is readily biodegradable and leaves no residue or hazardous waste product behind for clean-up or disposal. The ST-1000 delivery unit is intrinsically safe and ATEX Zone 2 rated with no electrical or moving parts.
“This new technology will assist vessel owners with their IMO 2020 compliance, given the increased need for bunker tank cleaning with the change of fuel grades and specifications. We believe the NanoVapor unit will greatly improve enclosed space crew safety and provide a better solution for shipowners as they face fuel emission deadlines,” said Steve Candito, Ecochlor’s CEO.
InterManager, an international trade association for the ship management sector, recently released an industry guideline sharing best practice submissions from crew with a mindset to reduce risks in enclosed spaces. As a long-term advocate for crew safety, Secretary General Kuba Szymanski commented: “InterManager is watching closely for the arrival of NanoVapor by Ecochlor as it promises to be break-through technology for Enclosed Space Procedures. Just imagine having a chemical which will be able to suppress toxic vapours emission – would that be the technological advance which would help our seafarers? We sincerely hope so! Coupled with naval architects more responsible attitude to the design of spaces which require humans to work in, this technology should provide a much safer environment for crew. We can’t wait for NanoVapor to be available for our ships!”
NanoVapor is finalizing testing with Lloyd’s Register for type approval with the expectation of completion by Marintec China 2019.
Media contact:
Ecochlor
Kathie Clark
Director of Corporate Communications
kathie.clark@ecochlor.com
About Ecochlor:
Ecochlor has sole market ownership of the patented chlorine dioxide (ClO2) ballast water management technology. Its ballast water management system has two-steps – filtration and chlorine dioxide. The treatment is not affected by variations in salinity, temperature, turbidity and vibration. It is reliable, simple to operate, has low power requirement with no retreatment or neutralization on discharge. The Ecochlor system is well-suited for mid-sized to the largest ships in the world and is IMO and USCG Type Approved. www.ecochlor.com
About NanoVapor:
NanoVapor’s breakthrough nanotechnology dramatically reduces the time needed to purge and gas-free a tank by up to 90% even with residual sludge remaining. It protects all health and safety requirements for tank entry, and can facilitate faster bunker tank cleaning procedures to satisfy the IMO global sulfur cap 2020. www.nanovapor.com